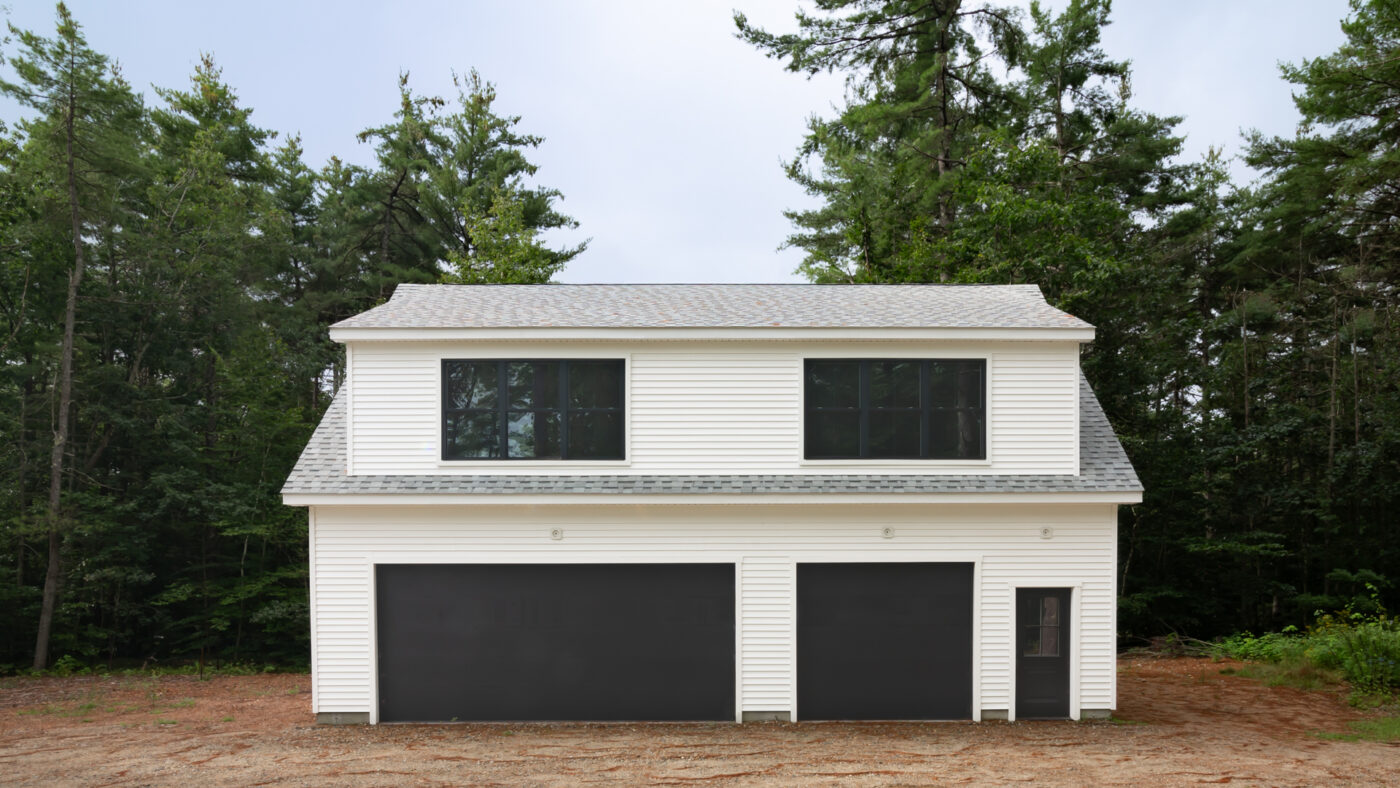
Garage Building Costs Budgeting for Your Project
Understanding Garage Building Costs: Planning Your Project Budget
Embarking on a garage construction project is an exciting endeavor, but it’s essential to have a clear understanding of the associated costs before breaking ground. From materials and labor to permits and unexpected expenses, here’s a comprehensive guide to budgeting for your garage building project.
Initial Planning and Design Costs
Before diving into construction, it’s crucial to allocate funds for initial planning and design expenses. This includes consulting with architects or designers to create blueprints, obtaining necessary permits from local authorities, and conducting site surveys to assess terrain and soil conditions. While these upfront costs may seem daunting, proper planning lays the groundwork for a successful and cost-effective construction process.
Material Selection and Procurement
The choice of materials plays a significant role in determining overall garage building costs. Factors such as size, style, and intended use of the garage will influence material selection and pricing. Common options include wood, metal, and concrete, each with its own set of pros and cons in terms of cost, durability, and aesthetics. Researching different material options and obtaining quotes from suppliers will help you make informed decisions while staying within your budget.
Labor and Construction Costs
Labor costs typically represent a significant portion of garage building expenses. Hiring skilled contractors or construction crews to handle foundation pouring, framing, roofing, and finishing work is essential for ensuring quality craftsmanship and timely project completion. Labor rates may vary depending on factors such as location, market demand, and the complexity of the project. Obtaining multiple bids from reputable contractors will help you compare costs and find the best value for your money.
Site Preparation and Excavation
Site preparation and excavation are critical steps in the garage building process and come with associated costs. This includes clearing vegetation, leveling the ground, and excavating trenches for foundation installation. Additional expenses may arise if special equipment, such as bulldozers or backhoes, is required to access the site or navigate challenging terrain. Factoring in these costs during the budgeting phase will prevent surprises down the road.
Utilities and Infrastructure
Connecting your new garage to existing utilities and infrastructure adds another layer of expense to your project budget. This includes installing electrical wiring, plumbing fixtures, and HVAC systems, as well as hooking up water, gas, and sewer lines if necessary. Depending on the location of your garage and proximity to utility connections, these costs can vary significantly. Consulting with local utility providers and obtaining estimates for installation and hookup fees will help you budget accordingly.
Finishing Touches and Amenities
Adding finishing touches and amenities to your garage can enhance its functionality, aesthetics, and value but also add to the overall cost. This may include insulation, drywall, flooring, lighting fixtures, shelving, and cabinetry, as well as exterior features such as doors, windows, and siding. While these extras may not be essential, they can significantly improve the usability and appeal of your garage. Prioritize your must-have amenities while keeping an eye on your budget to avoid